DIESEL AND HYDRAULIC OIL CLEANLINESS PROPOSAL
ASSISTING CELLULAR NETWORKS THROUGHOUT
THE ENTIRE AFRICAN CONTINENT
Through our official representative, Mr Bill Hearmon, we would like to take this opportunity to introduce your esteemed company to the tremendous benefits of depth filtration with regards to diesel, hydraulic and transmission oils.
Observation:
Due to atmospheric conditions, unreliability of diesel distribution/quality, algae build-up, sludging, acids and the harsh environment in which the cellular networks are operating throughout Africa, Filter Focus has engineered a product range to minimise diesel contamination and ensure that perfectly clean fuel is delivered to engine injectors, thereby substantially reducing maintenance costs, operating costs and the chance of break downs due to diesel or oil related failures.
Filter Focus realises the benefits of ensuring that higher cleanliness levels are achieved, to further reduce maintenance costs and unnecessary wear and tear caused through contaminated fuel. It is hereby suggested; that Filter Focus will endeavour to ensure that diesel cleanliness is kept at an optimal minimum level, through the implementation of ultra-fine filtration, fitted on each individual vehicle or generator set.
General Information:
The problems that are exposed through diesel contamination are definitely of great concern. One must bear in mind that we, in Africa, are placed in a position where we have to run high tech diesel vehicles specifically designed for European conditions, on sub-standard diesel brought about by contamination entering the diesel through down line contamination.
It is no secret that the diesel available in our country, and that of Africa, only just complies with the SABS and gazetted specifications as far as calorific values, viscosity and specific gravity is concerned. The trend to reduce sulphur in diesel has resulted in thinner and lighter diesels. However, the presence of contamination has been identified to present an even bigger problem. Due to these thinner and lighter diesels, it has become imperative that the ultra fine dirt particle and the water in-solution be removed from the fuel.
The below article will highlight the concerns of diesel contamination. These problems
CAN and HAVE been overcome with the use of depth filtration.
Although this problem is serious, the solution is relatively simple.
Filter Focus specialises in the field of ultra-fine depth filtration of diesel and oils. Through substantial research and development we have produced a filtration system that utilises traditional surface (area) filtration in conjunction with depth filtration. This process enables us to filter ALL particulate contaminants found in the diesel and hydraulic oil down to below 1 micron, as well as absorb water in solution down to below 20 parts per million.
Due to the extremely harsh and dusty conditions found in Africa, the diesel being utilised by vehicle operators is continuously becoming highly contaminated with dirt particles.
Area (surface) filters traditionally used by the industry to filter diesel are rated between 5 and 15 microns.
68% of all contaminants present in diesel are smaller than 5 microns.
The dynamic clearances of modern high-pressure injector systems are between 1 and 2 micron. It has therefore become strikingly apparent that traditional filters, which are presently being utilised, are inadequate, thereby making it necessary to employ a depth filter to achieve ultra-fine filtration. (Below 1-micron and water in solution to below 20 parts per million).
The primary aim of the modern Euro spec diesel motor is to reduce emissions.
-
In order to reduce emissions one needs a more complete combustion.
-
To obtain a more complete combustion a fine atomisation and efficient spray pattern is required
-
An increase in injector pressure is required in order to achieve a greater level of
automisation.
-
To obtain high injector pressures (2000 bar – 3500 bar); dynamic injector clearances and tolerances have been reduced.
The dynamic clearances of high-pressured injectors are between 1 and 2 micron, which means that a large percentage of the particles passing through the traditional OE filters are in actual fact causing on-going damage to the injectors, thereby resulting in substantial injector performance shifts.
Once the standard area filter becomes overloaded with contamination, the diesel is either by-passed or the pressure of the line forces the contaminants through the area filter and back into the diesel on the outlet side of the filter.
Injectors that are not operating at optimum levels will cause ineffective atomisation of diesel into the combustion chamber, resulting in an uneven and incomplete combustion. This leads to excessive carbon build up in the oil, as well as an increase in emissions.
Due to injectors not seating properly, dribble occurs and the un-atomised diesel results in unburned fuel to blow-by past the piston rings causing fuel dilution, which dramatically reduces the life and integrity of the engine oil.
Studies show that injector clearances and spray holes are eroded open by the large number of ultra-fine contaminants present in diesel, whilst being subjected to extremely high pressures. Larger spray holes result in atomised particles increasing in size, resulting in a prolonged burn period and poor combustion. Due to the prolonged burn period, exhaust gas temperatures have been observed to rise significantly, resulting in a reduction in power and turbo failures.
One must bear in mind that a diesel engine is simply an energy converter. By this we mean that it converts liquid diesel into heat energy, then into kinetic energy. Any excessive exhaust gas temperatures result in a loss of kinetic energy due to heat being released into atmosphere, via the exhaust system.
In some cases, exhaust gas temperatures that are supposed to be running at around 620 deg C are found to have escalated to over 800 deg C.
What is frightening is how quick this deterioration in injector performance occurs. The below test results prove this statement……
We ran tests on a Daimler Chrysler vehicle that had 3 064 km on the odometer. One can see on the attached dynamometer test that the performance shift that had already taken place within the first 3 000 km of the life of the engine, had been corrected, simply by ensuring that the diesel supply to the vehicle was spotlessly clean.
Through Caterpillar, we extended efficient engine life from an average of 3000 hours before engine failure, to an astounding 18000 hours. This was achieved on the Euro spec Huie system, which operates at 50 000-Psi injector pressure and experienced critical problems due to higher injector pressure and smaller dynamic clearances of injector spray nozzles. Please see the attached annexure from Barloworld / Caterpillar, “Filter 2000 technical reliability report” – Please excuse the grammatical errors as this is an internal Caterpillar report and therefore out of our control.
When purchasing a vehicle, selection is based on price, power output, fuel consumption, and maintenance costs. Performance shifts on injectors due to contamination in diesel will cause power output to decrease and emissions, fuel consumption and maintenance costs to increase.
Obviously injectors do have a life span, and such information is obtainable from the various manufacturers of injectors. Bosch SA have informed us that the high pressure Bosch injector system requires water in solution of below 50 parts per million.
Until the situation is reversed, not only the vehicle operators, but also our environment will continue suffering these negative consequences.
By “polishing” the diesel, which enters the fuel system, one is able to maintain emission levels, fuel consumption, as well as power output of a motor, within the manufacturer’s specification. The engine and injector life is extended thereby minimising performance shifts during the life of a vehicle. On countless vehicles that we have been involved with, we have been able to extend injector and engine life to well beyond manufacturers specification with minimal performance shifts.
Through our extensive dealings with the industry, we have come across many fuel “additives” that emulsify the free water and turn it into water in solution. This as we all know, is a deadly cocktail for any diesel engine.
It is common knowledge that diesel engines in Europe have much greater service intervals than are at present being enjoyed in South Africa and Africa. The only difference between the engines running overseas and those in our country is; the diesel being consumed and atmospheric conditions in which they operate. We have proven that by successfully cleaning the diesel, one also improves the integrity of the engine oil. If you look at the emission test that is attached, you will observe that there is a huge reduction is sulphur dioxide as well as particle emissions.
Filter Focus has run tests on a diesel engine whereby we fitted a FILTER 2000 depth filter to the diesel line only. After 35 000 km from new, the oil displayed a visual improvement by remaining clear and not going black due to soot contamination.
Unfortunately, the reality is that very few people know much about this on-going problem. Our endeavours are aimed at informing the vehicle manufacturers about the current situation facing this continent, as well as many other countries in the developing world. As can be seen, the solution to the problem is a relatively simple one.
Placing pressure on the refineries to clean up their act is a futile exercise. Our atmospheric conditions result in down-line contamination being one of the major causes of contaminants in diesel. Filter Focus is technically equipped to assist in sorting this problem out by “polishing” the diesel, in-line, just prior to entry into the injector pump. The last line of defence against contamination
We propose the following:
Filter Focus proposes to assist Cellular Network operations, through the installation of diesel and oil filters on vehicles and generator sets in operation throughout Africa and Southern Africa thereby:
-
Cleanliness level
-
For a prolonged period, we will keep the engines within manufacturers specifications with regards to power output, fuel consumption etc.
-
Substantially improve integrity of engine oil due to the reduction of unburned sulphurs and soot particulate.
-
Prolonged injector life.
-
Prolonged diesel pump life.
-
Protect turbo’s by keeping exhaust gas temperatures down to an acceptable level.
-
Dramatically reduce harmful exhaust emissions.
-
100% Reduction in downtime caused by diesel related failures.
-
Reduction in diesel and hydraulic oil consumption costs.
FILTER SPECIFICATIONS
Filter Name:
Filter 2000
Filter Type:
TC1
Manufactured:
South Africa
Distributor:
Filter Focus
Dimensions
Height
350mm
Diameter
130mm
Stand-off with bracket 150mm
Weight
4.7kg

Diesel flow rate
The TC-1 filter, with a diesel pressure of 3 bar will offer a flow rate of 7 Litres per minute or 420 Litres per hour. (ISO code: 14/12)
Pressure differential across the filter
The pressure differential across the TC1 unit is 0.22 bar.
Water absorption
Water in solution 150ml
Oil flow rate
The TC1 will make use of the internal sump pressure to filter, approximately 4% of the total oil content in the sump in 1 pass. The filter is used as a by-pass filter and will not affect the oil pressure or oil distribution within the motor.
Service intervals
The recommended service interval of the TC1 filter is 250-300 hours on both oil and diesel
Inlet and outlet of TC1
The inlet for the TC1 is situated offset from the centre on the bottom of the filter housing, and the outlet is situated in the centre, bottom of the filter housing.
Installation guide for diesel
The TC1 is installed after the original filter and before the injector pump. It is essential that the TC1 be installed after the lift pump to ensure that filtration takes place on the pressure side of the fuel system.
Installation Guide for oil
The oil pressure gallery contains two outlets, one with a blank plug and the other where the oil pressure sender unit is situated. The blank plug is removed and replaced with the take-off line for the TC1. The return line from the TC1 will connect into the sump drain plug.
Service Procedures
-
FILTER 2000 Depth filters are for the final polishing, and the removal of the ultra fine particles as well as the last of the remaining water that pass through conventional filters.
-
FILTER 2000 Depth Filters must always be installed last in line, and be preceded by good primary filter/water separators, or blocking will occur.
-
Caking on the ends of the elements is an indication of inadequate pre-filtration.
-
Inadequate primary water separation results in excessive water absorption and swollen elements.
-
FILTER 2000 elements are not intended to block in normal operation.
-
The particles are trapped on the fibres in the depth of the element by processes known as “inertial separation, interception and diffusion”.
-
It is advisable to periodically tear your used filter elements open to see how deep the dirt, shown by the discolouration of the paper (particles are too small to be seen by naked eye), has penetrated into the elements.
-
Dirt should not be allowed to penetrate more than 75% of the depth of the element.
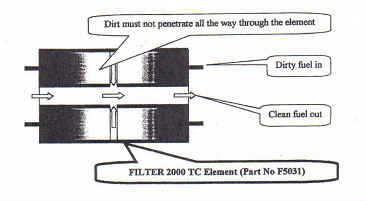
ELEMENT REPLACEMENT PROCEDURE
-
Ensure that the vehicle or machine is switched off and made safe.
-
Loosen the lid bolt, and unscrew and remove the entire filter element assembly from the filter housing.
-
Strip and reassemble the filter element assembly with new elements, ensuring that all parts are correctly in place.
-
Reinsert the filter element assembly in the filter housing, carefully screwing the return tube into the bottom of the filter housing.
-
Prime the filter housing before tightening down the bolt.
WHAT DOES ULTRA-FINE, DEPTH FILTRATION DO?
-
It removes all contamination particles down to below 1 micron in a single pass.
-
It removes water in solution down to below 20 parts per million or 0,002%
-
It contains 200 times more filter media than conventional filters. This means greater filtration and absorption of contaminants and water in solution.
-
Removes free sulphur.
-
Improves Fuel consumption, Power- and Torque outputs.
-
It has no bypass valve; therefore no contaminants are allowed to pass through to the injectors when the filter becomes blocked.
WHAT ARE THE BENEFITS OF INSTALLING ULTRA-FINE, DEPTH FILTRATION?
-
Extended injector life.
-
Improved fuel consumption due to cleaner burning fuel.
-
Extended engine life due to cleaner oil. Burning clean fuel means no build up of soot in the engine.
-
Reduced running cost.
-
Maintain fuel pump and injectors within calibration specification.
-
Stop injectors pitting due to water and contamination in fuel.
-
Power increase of up to 12% due to clean fuel.
-
Substantial saving on current maintenance and repair costs
-
ELIMINATION OF DOWNTIME DUE TO DIESEL RELATED FAILURES
Environmentally friendly. Elements can be incinerated
PLEASE NOTE THAT A FULL RANGE OF PRODUCT IS AVAILABLE TO CATER FOR ANY DIESEL CONSUMING ENGINE, REGARDLESS OF POWER OUTPUT. BULK FILTRATION SOLUTIONS ARE ALSO AVAILABLE AND DESIGNED ON REQUEST.
|
|
Tamarron Trading 126 (Pty) Ltd
(t/a) FILTER FOCUS
Reg. No. 2003/007994/07
P.O. Box 235
Gallo Manor 2052
South Africa
Tel:
+27 12 991 075
Fax: +27 11 804 5335
Cell:
+27 82 990 4443 (Bill Hearmon)
Email: bill@4gafrica.org
Cell:
+27 82 960 2913 (Craig FitzGerald)
Email: cfitz@filter2000.com
Director: G A FitzGerald
|